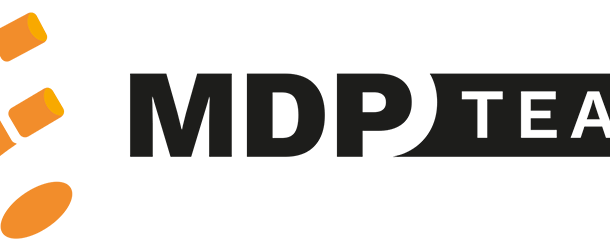
- The Group
- Project support
- Our technologies
- The Activity
Discover more than 20 years of expertise
choosing your market >
choosing your market >
choosing your market >
– 1 DUKANE VW5700 LPT Linear Vibration Machine
– 1 DUKANE i220 Ultrasonic Machine
Welding by vibration or ultrasound offers many advantages:
Welds can be made in a very short time, usually in a few seconds, whether by ultrasonics or vibration. Consequently, this increases the overall productivity of the manufacturing process.
Unlike other welding methods, ultrasonic welding does not require the addition of extra material. Therefore, adhesives, glues or solvents are not used. Instead, it uses ultrasonic energy to fuse the parts together. This makes the process more economical and environmentally friendly. Similarly, vibration welding works using only friction between the parts.
These welds create strong, durable joints by ensuring a molecular bond between the molecules of the plastic parts. As a result, they guarantee high mechanical strength of the weld, which can often be as strong or even stronger than the original materials.
An important advantage of these welds is that they do not involve intense heat as in other welding methods. As a result, there’s less risk of thermal deformation of parts, which is particularly beneficial for heat-sensitive plastic parts.
These welds are versatile, being suitable for a wide range of plastic materials. They are highly adaptable to commonly used thermoplastics such as PVC, PET, PP, PE, ABS and others. What’s more, they can weld parts of different shapes and sizes.
It’s easy to automate ultrasonic welding by integrating this technique into automated processes. By programming ultrasonic welding machines, it is therefore, possible to perform precise and repeatable welding operations, delivering consistent results and reducing labor costs.
No potentially polluting chemicals or solvents are used in these welding methods. As a result, these methods are environmentally friendly, reducing risks to workers’ health and adverse effects on the ecosystem.
Both are used in a variety of industries, including automotive, industrial, medical, luxury goods, cosmetics, aerospace and defense. They are suitable for assembling plastic parts of different shapes and sizes, offering great flexibility for a wide range of applications.
With the arrival of these two new welding machines, MDP TEAM is more than ever at your disposal to meet all your prototyping or small/medium series injection molding needs. Our team is fully committed to listening carefully to your projects and providing tailor-made solutions.